A Few Pictures
The stool is made from 2x10 Douglas fir—all except the top. The original top was made from 2x10 material but the top began to crack during the build. So a substitute was made by gluing together 2 pieces of 1x10 (actual dimensions, 3/4" x 9 1/4") Douglas fir.
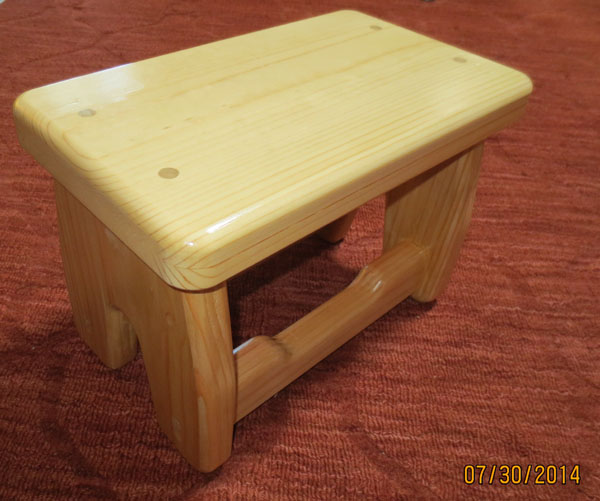
Notice the 1/2" dowels in the top that secure the top to the base. No metal was used in the construction of the stool. Dowels were used at critical places to give the joints strength.
The side view, below, shows a support piece below the centerline of the top, and stretchers near the bottom on both sides of the legs. The cutout in each stretcher serves two purposes:
- It's decorative
- It provides a place to hook your toes so that you can drag the stool across a carpeted floor with your foot
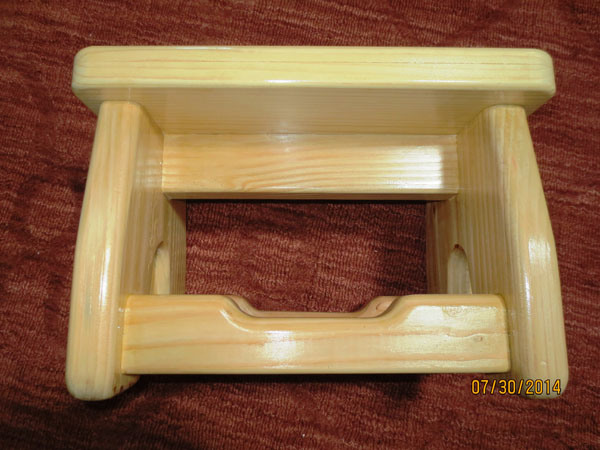
An end view is shown below. Notice the placement of the 1/2" dowels: one into the support below the top and one into each stretcher.
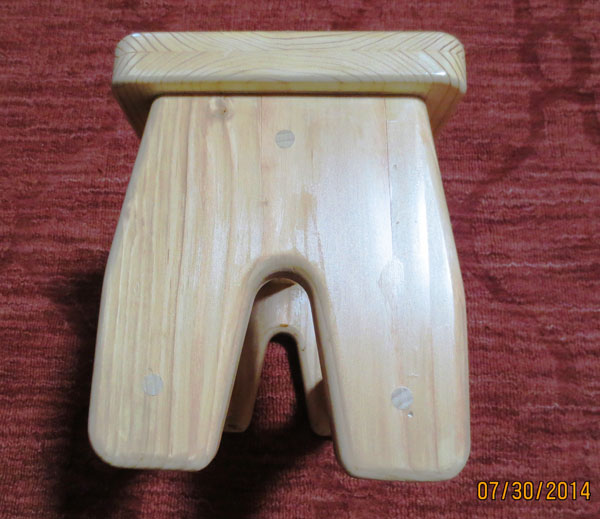
Some of the Particulars
- Height: 11"
- Dimensions of the top: 9 1/4" x 16"
- All edges are rounded over
- The stool is finished with clear gloss polyurethane
- Glue: Titebond II or equivalent
No drawing was created for this project. It was built "on the fly." If you'd like to build a stool like this one, just use the pictures and the other information provided here to estimate your needed dimensions.
A 3/8" round-over was used along the top edges of the top, all edges of the legs, and the top edges of the stretchers. A 1/4" round-over was used along all other edges: the bottom edges of the top, the bottom edges of the support piece under the top, and the bottom edges of the stretchers.
The round-overs on the bottoms of the legs, together with the smooth finish provided by the polyurethane, allow the stool to slide easily over a carpeted floor. That means the stool is easy to slide under a tall bed and pull back again by using just your toes.
As mentioned earlier, two pieces of 1x10 were glued together to create the top. You can see in the bottom picture that the end grain of the two pieces that make up the top are arranged in opposite directions. This was done because, when wood warps, the curved grain tends to get straighter so that the centers of the two pieces tend to want to separate. I believe the glue bond is stronger in this configuration than if the outer edges were trying to separate.